Boost Your Manufacturing Quality with State-of-the-Art Metal Stamping Providers
Boost Your Manufacturing Quality with State-of-the-Art Metal Stamping Providers
Blog Article
Advanced Techniques in Metal Stamping for Precision Production
As markets consistently require better tolerances and elaborate styles in their metal elements, the mission for sophisticated strategies in metal stamping has actually magnified. From the application of sophisticated multi-stage stamping processes to the combination of innovative automation innovations, the landscape of metal stamping is undertaking a profound makeover.
Advanced Multi-Stage Stamping Processes
Discussing the ins and outs of advanced multi-stage stamping processes reveals the sophisticated techniques employed in modern production methods. Metal Stamping. Multi-stage stamping is a complicated procedure that includes multiple actions to change a level sheet of steel right into a last stamped product. Using progressive dies, where various procedures are performed at each stage of the marking process, permits high precision and effectiveness in the production of elaborate steel parts
Throughout the initial phases of multi-stage marking, the level metal sheet is fed right into the stamping press, where a collection of passes away are used to reduce and shape the product. Succeeding stages include additional forming, bending, and punching procedures to more improve the component. Each phase is thoroughly created to build on the previous one, causing the production of complicated geometries with limited resistances.
Advanced multi-stage stamping processes call for a high degree of experience and precision to guarantee the quality and uniformity of the stamped parts. By using innovative machinery and tooling, suppliers can create a large range of metal components with effectiveness and precision.
Precision Tooling Innovations
Accuracy tooling innovations have changed the steel stamping market, improving effectiveness and high quality in manufacturing processes. CNC systems allow for intricate styles to be translated straight right into tooling, making sure accuracy and repeatability in the stamping process.
Moreover, the integration of sensing units and real-time monitoring abilities in precision tooling has made it possible for suppliers to find and deal with problems promptly, reducing downtime and lowering scrap prices. By integrating wise technology into tooling, drivers can enhance criteria such as pressure, rate, and positioning during the marking procedure, causing boosted product top quality and boosted productivity.
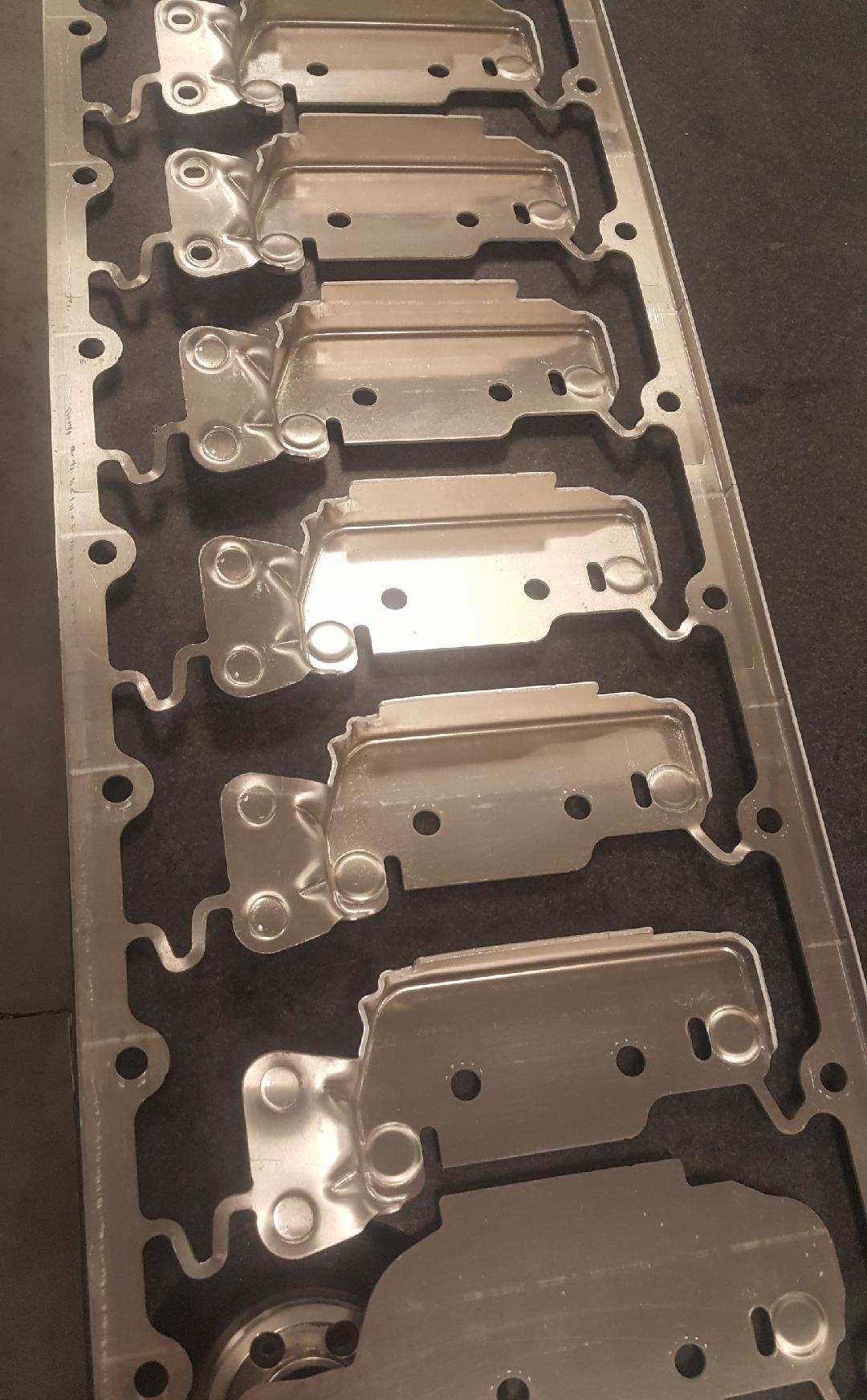
Automation in Metal Stamping
The advancement of precision tooling developments in the metal marking sector has actually led the way for considerable improvements in automation, changing the manufacturing landscape towards increased performance and performance. Metal Stamping. Automation in steel stamping includes making use of advanced machinery and robotics to carry out numerous tasks commonly executed by human operators. This shift towards automation uses various benefits, consisting of enhanced accuracy, faster production cycles, and decreased labor prices
One key element of automation in steel stamping is the implementation of computer numerical control (CNC) systems, which enable precise control over the stamping procedure. CNC technology permits the production of facility and elaborate metal get rid of constant check out this site high quality. Furthermore, automated systems can be configured to run constantly, bring about greater output prices and shorter preparations.
Additionally, automation boosts office security by decreasing hand-operated handling of heavy materials and lessening the danger of crashes (Metal Stamping). As making industries remain to embrace automation, the future of metal marking holds excellent assurance for even greater performance and innovation
High-Speed Stamping Techniques
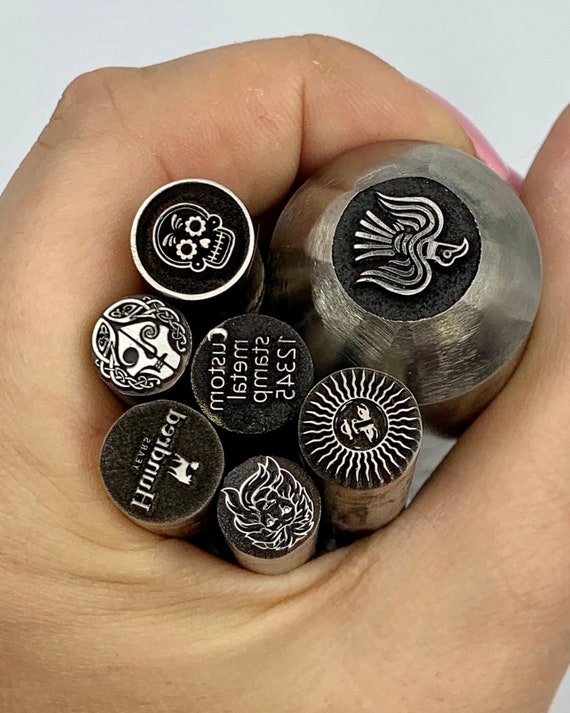
One of the key benefits of high-speed stamping methods is the capability to create a large volume of parts in a much shorter amount of time contrasted to traditional stamping techniques. This increased efficiency not only allows producers to fulfill limited production target dates but likewise makes it possible for expense savings via economic situations of range. In addition, high-speed marking can help in reducing product waste by optimizing the material usage throughout the stamping procedure.
Additionally, high-speed stamping techniques usually incorporate cutting-edge attributes such as quick die modification systems and real-time tracking capacities, even more boosting the overall performance and flexibility of the steel marking process. As modern technology proceeds to development, high-speed stamping is anticipated to play a crucial duty in driving the future of accuracy manufacturing.
Top Quality Control in Stamping Procedures
Efficient quality assurance steps are important for guaranteeing the dependability and consistency of steel marking procedures. Quality additional reading assurance in stamping operations includes a collection of systematic processes targeted at detecting and avoiding flaws in the manufactured parts. One important facet of high quality control in metal marking is making use of innovative examination techniques such as optical inspection systems and coordinate measuring makers (CMMs) to validate the measurements and tolerances of stamped components.
Furthermore, top quality control procedures in stamping operations usually consist of the application of analytical procedure control (SPC) approaches to monitor the manufacturing procedure in real-time and guarantee that it stays within appropriate limits. By evaluating information and identifying trends, makers can proactively address any variances from the wanted high quality criteria.
Additionally, high quality control in steel marking procedures also involves comprehensive product screening to ensure that the raw materials utilized satisfy the called for requirements for the marking process. This may include conducting material hardness tests, tensile toughness examinations, and dimensional inspections to guarantee the quality and integrity of the link stamped elements. In general, carrying out durable quality assurance steps is important for accomplishing top notch stamped components constantly.
Final Thought
In verdict, progressed strategies in steel marking play a critical duty in accuracy manufacturing procedures. Via multi-stage marking processes, innovative tooling solutions, automation, high-speed techniques, and strenuous quality assurance measures, suppliers can achieve higher degrees of precision and effectiveness in their operations. These innovations in steel marking innovation have made it possible for firms to create complex parts with tight resistances, eventually resulting in improved item high quality and client satisfaction in the production market.
Report this page